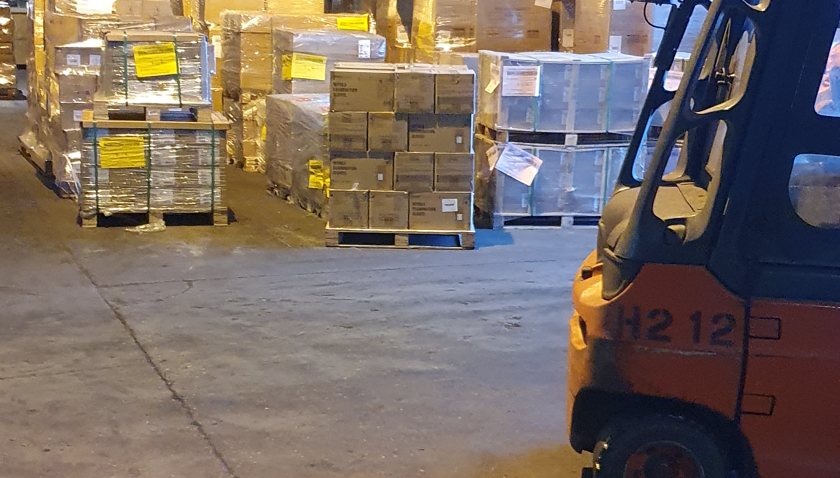
Adapting Supply Chain Strategies: The Shift from Just-In-Time to Just-In-Case
Supply chain management has always been a crucial aspect of businesses, and in today’s dynamic environment, it has become more critical than ever. The recent global challenges, like the COVID-19 pandemic, have exposed the limitations of Just-In-Time (JIT) methodologies, and businesses are now considering shifting to more resilient approaches like Just-In-Case (JIC).
In this blog post, we will discuss why and how businesses should consider shifting their supply chain policies from JIT to JIC, especially in the face of global uncertainties and market fluctuations.
The Evolution from JIT to JIC
Just-In-Time, a strategy popularized by Taiichi Ohno for Toyota, revolutionized supply chain management with its lean, demand-driven approach. JIT involves maintaining minimal inventory, relying on precise delivery of goods, and streamlining production processes to optimize cost and reduce storage needs.
However, recent global challenges, like the COVID-19 pandemic, have exposed the limitations of JIT, especially its vulnerability to unexpected disruptions. This has prompted a strategic pivot to Just-In-Case. This methodology emphasizes preparedness and resilience in supply chain operations.
Understanding JIT: Efficiency at Its Core
JIT, with its roots in lean manufacturing, focuses on reducing waste and increasing efficiency. While this approach optimizes cost and reduces storage needs, it depends on predictable demand and stable supply channels.
The Rise of JIC: A Response to Uncertainty
JIC emerges due to the increasing unpredictability of global supply chains. This approach prioritizes having surplus inventory and more robust safety nets to handle sudden demand spikes or supply shortages. JIC is about planning for various scenarios, including those that are unlikely but could have significant impacts.
Why the Shift is Necessary
- Increased Market Volatility: The global market has seen unprecedented fluctuations, making demand forecasting more challenging.
- Supply Chain Disruptions: Natural disasters, political unrest, and pandemics have highlighted the fragility of tightly connected global supply chains.
- Consumer Behaviour Shifts: The digital era and the pandemic have rapidly changed consumer expectations, demanding more agility from suppliers.
Balancing JIT and JIC: Finding the Middle Ground
The goal isn’t to abandon JIT entirely but to integrate JIC principles for a more balanced approach. This hybrid model involves maintaining some level of inventory while still leveraging JIT’s efficiency where feasible. It’s about being agile enough to switch between these methodologies based on real-time market and environmental signals.
Implementing JIC: Practical Steps for Businesses
- Diversify Suppliers: Relying on a single supplier or region can be risky. Diversifying suppliers geographically can mitigate risks.
- Invest in Technology: Advanced analytics and AI can provide better demand forecasting and risk assessment insights.
- Build Strategic Inventory: Maintain a buffer stock to cover demand during unexpected disruptions.
- Develop Flexible Operations: Create adaptable manufacturing processes that can quickly respond to changes in demand.
The Role of Technology in Facilitating the Shift
Technology plays a pivotal role in transitioning from JIT to JIC. Tools like AI, machine learning, and predictive analytics can help businesses forecast demand more accurately, identify potential supply chain risks, and make informed decisions about inventory levels.
Goodada’s Role in Enhancing JIC Strategies
So, incorporating Goodada’s Quality Control Inspection services is a game-changer for firms adopting a JIC approach. These services ensure product quality and consistency, which are crucial in managing risk and maintaining customer trust. Therefore, by proactively addressing quality issues, Goodada’s inspections are instrumental in building a resilient and reliable supply chain, which is essential in a JIC framework.
Case Studies: Successful JIC Implementations
Several companies have successfully integrated JIC principles into their supply chain management. These case studies demonstrate how a balanced approach can increase resilience without significantly compromising efficiency.
Preparing for the Future
The shift from JIT to JIC isn’t just a reaction to recent challenges; it’s a strategic move towards future-proofing businesses. By embracing flexibility and preparedness, companies can navigate the uncertain waters of global supply chains more effectively. The key is to find the right balance that suits each business’s unique needs and market dynamics.
Conclusion
In conclusion, transitioning from Just-In-Time to Just-In-Case in supply chain management is a necessary evolution in response to the changing global landscape. By adopting a more resilient and flexible approach, businesses can better prepare for unforeseen challenges, ensuring sustainability and success in the long term.
So, for more information about Just In Time and QC inspections, contact:
Contact Person: Aidan Conaty
Mobile- Messenger (Click to Connect)
Laptop / PC (Click to Connect)
Phone:(Europe/ Rest of the World) +353 1 885 3919 ; (UK) +44.020.3287.2990 ; (North America) +1.518.290.6604